Your cart is currently empty!
Forging Brass Burner
Built to withstand the toughest conditions, our forged brass burners offer superior strength, durability, and heat resistance. The forging process enhances the structural integrity, making these burners ideal for demanding applications
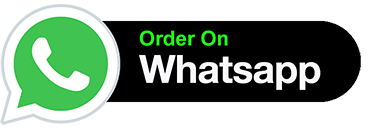
Description
The Craftsmanship Behind Brass Burner Forging
The process of forging brass burners is a meticulous art that combines skilled craftsmanship with an adherence to high-quality materials. At Daiwik Appliance, the journey begins with selecting superior brass, an alloy primarily composed of copper and zinc, known for its excellent thermal conductivity, corrosion resistance, and overall durability. This ensures that the finished product not only performs efficiently but also stands the test of time in various cooking environments.
The forging techniques employed in the manufacturing of brass burners involve applying intense pressure to reshape the brass into its desired form. This may include methods such as hot forging, where heated brass is molded with precision, and cold forging, which allows for enhanced surface finish and tighter tolerances. Each technique plays a critical role in the overall integrity of the burner, as the process can significantly affect mechanical properties such as strength and hardness, thus influencing functionality.
Precision is paramount in creating brass burners, as each piece must fit perfectly within the assembly of the cooking appliance. Ensuring that every burner is shaped accurately not only enhances the aesthetic appeal of the product but also its efficiency. When designing a burner, careful consideration is given to features such as flame distribution and heat retention. This level of attention leads to improved cooking performance, catering to the varying demands of diverse culinary practices.
The blend of traditional forging methods with modern technology further elevates the craftsmanship at Daiwik Appliance. By leveraging advancements in machinery and techniques, skilled artisans can achieve unparalleled quality while maintaining the authenticity of hand-forged elements. This harmonious integration exemplifies the dedication to excellence that defines the brass burner forging process, underscoring the importance of expertise and innovation in creating outstanding kitchen appliances.
Quality Control and Testing of Brass Burners
At Daiwik Appliance, the quality control and testing of brass burners are paramount to ensuring that every product meets the highest standards of safety, reliability, and performance. The process begins with meticulous inspections of raw materials to confirm that they comply with industry specifications and suitability for high-quality brass burners. Each batch of brass is examined for its chemical composition, strength, and potential impurities, which could compromise the integrity of the finished product.
Once the raw materials pass inspection, the brass burners undergo a series of testing phases. Each burner is subjected to pressure tests to evaluate its performance under various operating conditions. These tests determine the burner’s ability to withstand high heat and pressure, crucial factors for safe and effective operation. Additionally, flame pattern analysis is conducted to ensure an even and efficient combustion, which is integral to cooking efficiency and safety.
Daiwik Appliance adheres to various national and international standards, guaranteeing compliance with necessary safety regulations. Certifications, such as ISO and other relevant industry standards, are attained to reinforce the quality claim of the brass burners. These certifications not only validate the manufacturing processes but also instill confidence in consumers regarding the durability and reliability of the products they purchase.
Moreover, feedback from customers is actively sought and analyzed, forming a critical part of the continuous improvement cycle for products. This input is invaluable in identifying potential areas for enhancement and innovation in burner design and functionality. Daiwik’s commitment to embracing customer insights demonstrates a dedication not only to producing high-quality brass burners but also to constantly evolving in response to the needs of the market.
Reviews
There are no reviews yet.